前回、新幹線を当コラムで取り上げましたが、それは新幹線の「夢」の部分でした。今回は技術的な分野、特に「事故」について取り上げてみたいと思います。
新幹線の技術的な問題による事故といえば、記憶に新しいのが2017年12月11日に発生した東海道・山陽新幹線「のぞみ34号」の台車ひび割れ事件です。幸いにしてこの「事件」は「事故」にまでは至りませんでしたが、技術的観点からは大きな問題を内包していると考えられます。
この事件は、走行中の異常を察知した乗務員の機転で名古屋駅で点検を行い、事故を未然に防ぐことができました。もし、そのまま走行していたら車両が脱線し、大事故になっていたと考えられます。では、技術的観点から何が問題だったのでしょう?
一番大きな問題は、台車の製造方法が適切ではなかったという点です。様々な報道から、当該車両の台車は、設計時に考慮すべきであった安全性を軽視した製造を行っていたようです。強度を保つために必要な部品の厚みが、製造段階で薄く加工されてしまっていたのです。本来なら勝手に加工することは許さないのですが、これまでの新幹線を製作してきた経験から他の部品との結合に用いる溶接をやりやすくするために、生産現場はこの部品の厚みを薄くしても問題ないと判断したようです。
また、溶接技術者には常識ですが、溶接したところには残留応力として知られている応力が発生します。通常は、その応力を除去する処理を行ないますが、その処理も行なわれていませんでした。さらに、そこには走行による繰り返し荷重が重なって作用したために設計値以上の荷重がかかって部品にひびが発生し、そのひびが運転を繰り返すうちに大きくなり、遂には台車の変形を招き、走行に支障が出てしまったのです。
国土交通省の資料によれば、この「重大インシデント」の原因を「疲労亀裂」と結論づけています。本資料に掲載された図を引用していますが、万が一があってはならない部品を設計図面通りではなく加工して組み立てた結果がこの事故です。製造現場の責任は重大だと言わざるを得ません。
機械エンジニアは、製品の強度計算を行い、それに安全率を乗じて設計図面とします。安全率が高ければ高いほど製品の安全性は向上しますが、重量が増加したり、コスト面で不利になります。そこで製品には「寿命」を設けます。「1000時間を超えて使用してはならない」と設計図面に書いてあれば、その部品は1000時間を超えて使用してはならないのです。交換を前提として製品作りを行えば、重量とコストの増加も最小限に抑えることができます。これがものづくりの現場の考え方です。
しかし今回の事件では、設計図面通りに部品の製造がなされなかったことが事故を招きました。私たちはこの事件を教訓として、ものづくりの安全性、ひいては日本製品の安全性の向上に日夜努めたいと思います。「日本品質」が世界で認められているのは、先人たちのたゆまぬ努力の賜物です。私は本校から羽ばたくエンジニアの卵たちも、この伝統を引き継いで欲しいと願っています。
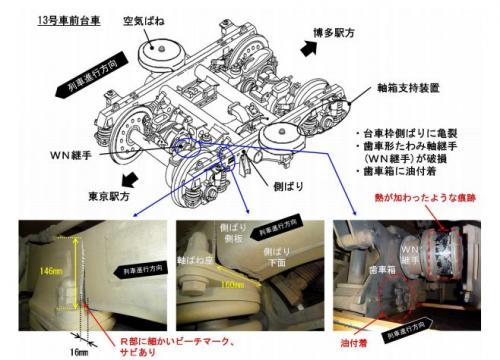 |
「のぞみ34号」の問題の台車(国土交通省「重大インシデント報告書」より引用) |
(文責:精密機械技術科 田中 誠一郎)